What used to be guesswork for metalworkers is today a labor-intensive job, that of estimating production times within the metalworking industry. But artificial intelligence and machine learning are going to change that. Really; we’re reverting back to predicting thanks to these developments. More accurate and therefore more reliable than ever. Too good to be true? Read this blog and discover the future of quoting and planning within the metalworking industry.
First, back in history for a moment. Decades ago, metalworkers specialized in a small number of operations such as laser cutting, welding or the sawing of beams. As specialists, they could estimate the production time of that work on the back of a beer coaster. So with guesswork
There is still a generation of metalworkers from that era. They have an admirable sense of how to determine the production time associated with processing a certain amount of kilograms of metal. However, due to the increasing diversity of operations, this is almost impossible to do in practice. Take laser cutting: making many complex shapes is different than cutting out a large square. The kilos are the same, but the production times involved are really different.
The importance of reliably estimating prices and lead times
It has become increasingly important within the supply chain for metalworkers to be able to estimate reliably. This is primarily due to small margins, which are under pressure due to competition. The key is to offer increasingly competitive prices. Then it’s not helpful if you start overestimating.
Accuracy is also required because the production times you estimate have implications for the subsequent production process. The time estimate determines which metalworking machine you reserve when. And if it reduces capacity on the factory floor, it has a detrimental effect on every single request that comes in. Hence, avoid.
Third, there is a growing emphasis on shorter time-to-market in the supply chain. As a result, there are fewer on-site stocks and just-in-time delivery is more or less a requirement. This means that the estimates you make as a metalworker will affect your delivery time. Misjudge? Then your delivery time may easily become too long. And that negatively impacts the supply chain. Due to incorrect estimation, the products may also be sitting on your production floor waiting for you. All of which are inconvenient.
Estimating does not need to be labor intensive
That’s why it’s so important to be able to estimate with accuracy. The time for guesswork is over. Instead, other techniques have taken over. In part, CAM systems help to estimate because they have knowledge of the technical specifications of machines and know what tasks machines need to perform. From there, they can then associate times with that. That way you can get very accurate estimates from CAM systems.
The disadvantage of this: it is very labor intensive. For people are still in charge. In this process, the estimator has become a kind of disc jockey. He browses through all those CAD files to get production times out of them. He then crams those into Excel and/or the ERP system so that he can eventually produce quotations. A time-consuming process, especially as the diversity of operations has increased. This causes the estimator to take longer to produce a quotation – and customers to wait longer for their prices.
We are still talking about estimating rather than predicting. While guessing and gut feeling were still the most useful ways to make predictions based on kilograms, estimators now have to use complicated formulas to estimate the times of the various production steps.
Faster metalworking machines make time estimation more difficult
There is another development that complicates this process. Machines have become faster and faster. No matter how much knowledge and experience estimators have, this makes it increasingly difficult for them to estimate production times. Especially since the bottleneck, where the production process is slowest, keeps shifting. For example, what is occurring now; cutting machines can cut so fast, that loading a plate, or getting the cut products out, takes much longer than the cutting itself.
You can use technology for that, but once you’ve done that, getting the plate to the machine is the slowest factor in the process. So that changes nothing for a estimator. Sometimes he is estimating at a detailed level how much time cutting takes, while losing sight of the fact that transporting the products to the next workstation can take up to five to ten minutes.
Big data drives efficiency improvements within the metalworking industry
Fortunately, change is happening at a rapid pace. Let’s start with the metalworking machines themselves. In the past, these worked “alone” and provided little feedback on the production process. Now they are sharing more and more information about what they are doing; we call those events. This is partly because machines today are connected to the factory computer network. So they can not only receive input, but also send out events that tell exactly what the machine is doing.
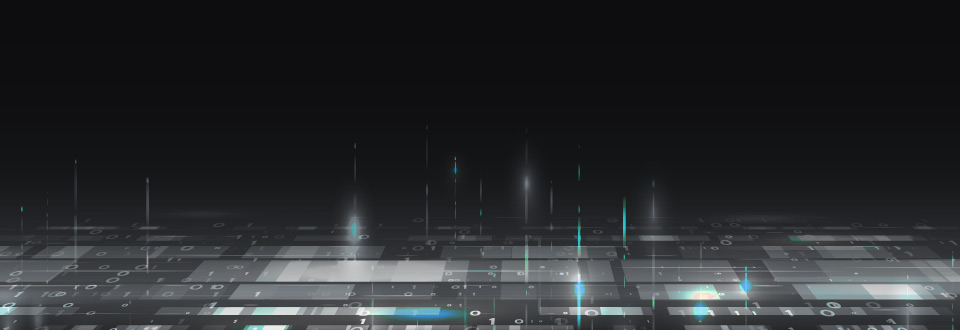
This means that the behavior of the machine has become observable. If you capture events, you can very well use them to learn more and more about the working speed and loading time of machines. But also how often a machine has downtime. Once we capture those events as important information, big data is created. And the more you have at your disposal as a metalworker, the more valuable. Because you can then use all that information for a new generation of algorithms.
Digital twin provides process optimization on the work floor
This fuels another accelerated development. As the machine is connected to the network and transmits a lot of information, a new form of software has emerged: digital twin. This digital twin, a virtual representation of reality, runs on the server and mimics the behavior of the machine on the work floor. All events that the machine ‘spits out’, information about the current status of the machining process for example, can be extracted in this virtual environment.
And so gradually the entire metalworking plant is getting a reproduction in the virtual world – in the form of digital twins. Those twins can be about anything: the current status of machines, the location of autonomous driving carts and even the operators on the factory floor can get a digital twin thanks to cameras. You can then apply algorithms to that, which, for example, continuously monitor the safety of operators and automatically trigger an alarm if necessary. Even entire business processes or affairs regarding the factory as a whole, including transport and energy consumption, can be embodied in a digital twin.
Automated business processes within the metalworking industry thanks to data in the cloud
While digital twins are abstract representations and thus usually not visible on a screen, they are very valuable in communication between different machines – even if they belong to other companies in the chain. Normally these machines converse in their own dialect, but digital twins produce standardized events, creating “event streams”. The great thing is that you can subscribe to those streams with other parts of your production process. By capturing all events, you can stream the entire plant through time. Exactly as if you were playing recorded music.
Plant behavior in playback form is the future. And to make it even more inventive, business processes can subscribe to those streams as subscribers. So when an event occurs, you can thereby automatically start a new process or make a decision at a certain point in time. These streams thus grow into an important basis for developing automated business processes and decisions.
At the moment, such technologies, like digital twins or event subscriptions, operate mainly on computer systems within a factory. However, the exact same services are now available in the cloud. This allows you to send events to the cloud, include big data there and automate business processes. Another advantage; you can connect factories together in the cloud much more easily than you can connect to the infrastructure within the very walls of a factory.
From data driven to event driven metalworking plants
The farewell to conventional thinking, in terms ERP systems, is imminent. Centralizing data is still in the lead today, making that data reusable in factories. That certainly has its value, but it mainly creates data-driven processes. That paradigm will rapidly depart the industry.
Instead of being data-driven, metalworkers are going to set up their factories event-driven. The big advantage? By subscribing multiple business processes to events, a plant can respond to incidents in much more real time, and in doing so they are less dependent on the central database. After all, the event already contains the data that is needed.
Where previously the ERP system had an important role, another technology is taking over: Enterprise Service Bus. This architectural software construct allows you to capture events, observe them, and allow processes to subscribe to those events. It allows you to set up business processes much more robustly and in real time. Everything that happens in your factory becomes observable within the digital world.
From estimating to predicting thanks to cobots and AI
This is what today’s technology makes possible. This is the foundation that allows you to go from estimating to predicting as a metalworker. Even as machines are becoming more capable, faster, and the bottleneck is shifting as a result. Even as cobots are increasingly taking on some of the work of operators, so the speed of the process changes and realistic estimation of production times becomes even more difficult. But in the new digital world, cobots are also connected to the network, and they too have a digital twin, which means that their work too can be observed and estimated more accurately in time.
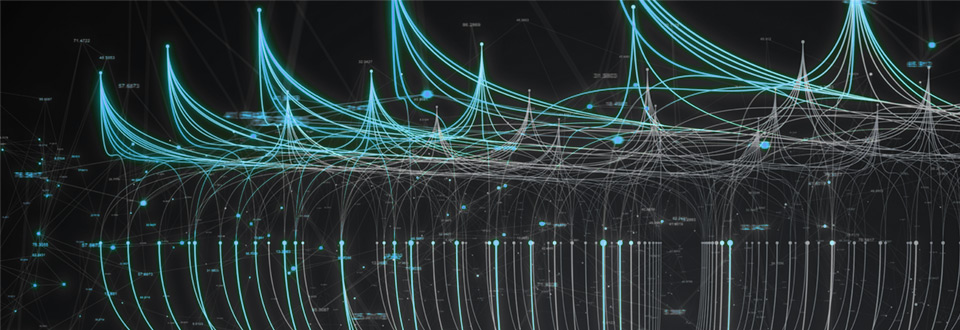
It is the power of artificial intelligence. As humans, we cannot beat the computer. And that’s because we can make the computer learn like humans learn, but faster. For that, we do need to train him. Preferably continuously. That requires a lot of data. So how do we teach a computer to play chess? By digitizing all the chess games played and feeding them to the computer. That’s how it learns chess step by step. This is even faster if you let two computers play chess against each other; then incredibly reliable algorithms are created in a relatively short time. That’s the big advantage: the computer learns much faster than humans. You can train those 24/7 without getting tired.
This creates a neural network – an imitation of how the human brain works – synchronized in software. Training that process is called machine learning. By using big data, it is possible today to properly train those neural networks. And as it is better trained, it produces better and better predictions. We no longer call these estimates because we no longer use formulas. Instead, we predict the future based on the past. Because the data you train the model with is always about the past. So now we are applying this strong piece of modern technology to the metalworking industry.
Continuous self-learning system instead of excel sheets
There are three different technologies that will enable metalworkers to move from estimating to predicting: big data, event-driven factory design (observable factory) and artificial intelligence. When it comes to quotations and work preparation, these three developments mean that we as humans no longer have to work with excel sheets to estimate production times.
We can instead set up a continuous self-learning system, which allows the estimator to predict production times much more reliably. No longer are metalworkers dependent on the availability of people’s knowledge and skills. The complete past and present of their factory are contained in big data, which they can always use in the future to improve algorithms and even make new discoveries.
This completes the story. Because the way the digital world works remains similar to how specialists used to determine the production times of their operations. It’s still a prediction, only the guesswork has been replaced by a computer that uses much more data. The difference? Very high accuracy – and that’s what the metalworker wants.